Fertigung
Wir fertigen vom Prototyp bis zur Großserie Kunststoffteile im Full-Service, d.h. von der Konstruktion bis zur Montage und Oberflächenveredelung.
Innovative Fertigungstechnologie
von FUNK DREIDIMENSIONAL
Die Firma FUNK DREIDIMENSIONAL ist spezialisiert auf die Produktion hochpräziser Kunststoffteile in allen gängigen technischen Kunststoffen. Auch im Bereich 2K und bei Hochleistungskunststoffen sind wir ein zuverlässiger Partner. Mit unserem nach IATF16949 zertifiziertem Produktionsbereich bieten wir serienreife Lösungen für komplexe Baugruppen, Klein- und Kleinstserien bis hin zum Einzelteil an. In unserer Fertigung werden aber genauso Teile für unterschiedliche Branchen in millionenfacher Stückzahl gefertigt.
FUNK DREIDIMENSIONAL fertigt technische Kunststoffteile wie Lichtleiter, Zahnräder, Gehäuseteile, Filtergehäuse und Verkleidungen für verschiedene Branchen wie Automotive, Medizintechnik, Dentaltechnik, Maschinenbau, Möbelindustrie sowie Energie- und Messtechnik. Dabei können alle thermoplastischen Kunststoffe verwendet werden.
Die besondere Stärke von FUNK DREIDIMENSIONAL liegt in der schnellen und flexiblen Reaktion auf Änderungen oder Probleme dank Entwicklung, Modellbau, Werkzeugbau und Fertigung unter einem Dach. Die einzelnen Abteilungen sind gut vernetzt und unsere qualifizierten Mitarbeiter berücksichtigen bereits bei der Konstruktion und im Werkzeugbau die späteren Anforderungen der Fertigung. Dadurch sind sie schneller, flexibler und spontaner als so mancher Mitbewerber.
Prinzipiell verarbeiten wir alle thermoplastischen Kunststoffe – ob Standardkunststoff, technischer Kunststoff oder Hochleistungskunststoff. Genauso flexibel wie bei der Werkstoffauswahl sind wir bei der Fertigung der Stückzahlen. Sie können bei uns Prototypen und Kleinserien genauso wie Großserien mit millionenstarken Stückzahlen in Auftrag geben.
Ausschnitt aus unserem Portfolio:
- Lichtleiter
- Zahnräder, Kugelführungen
- Bauteilaufnahmen
- Gehäuseteile, Filtergehäuse
- Verkleidungen Abdeckkappen, Schutzkappen
- Cupholder, Ablagefächer
- Fahrzeugtische, Bustische, Tablethalter
- Gehäusefüße, Griffleisten
- Abstreifer
- Displayaufnahmen
- Strömungsrahmen
- Kleiderbügel, Haken
- Gehäuse für Linearführungen
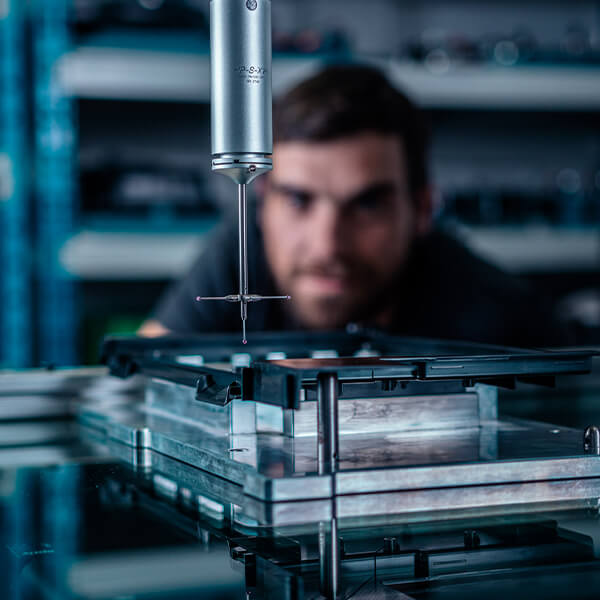
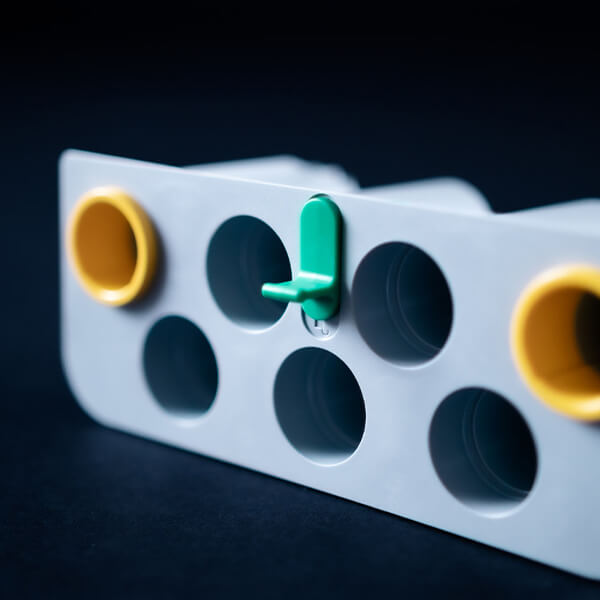
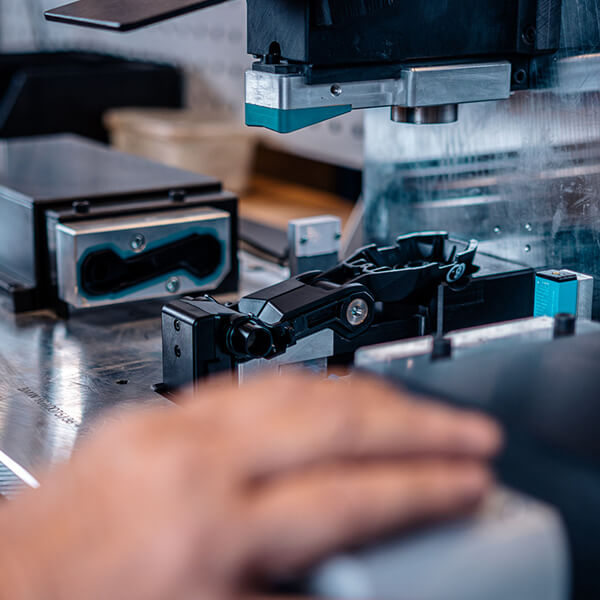
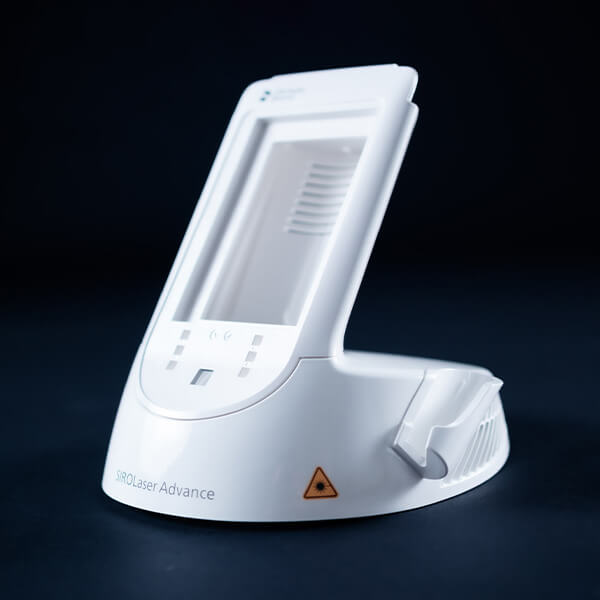
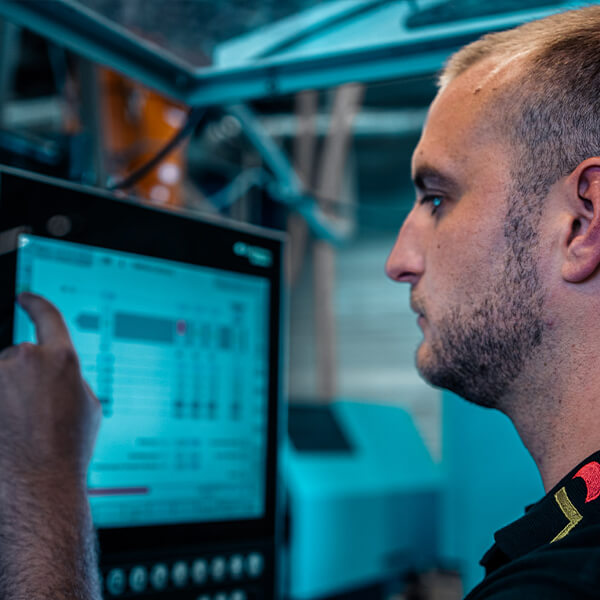
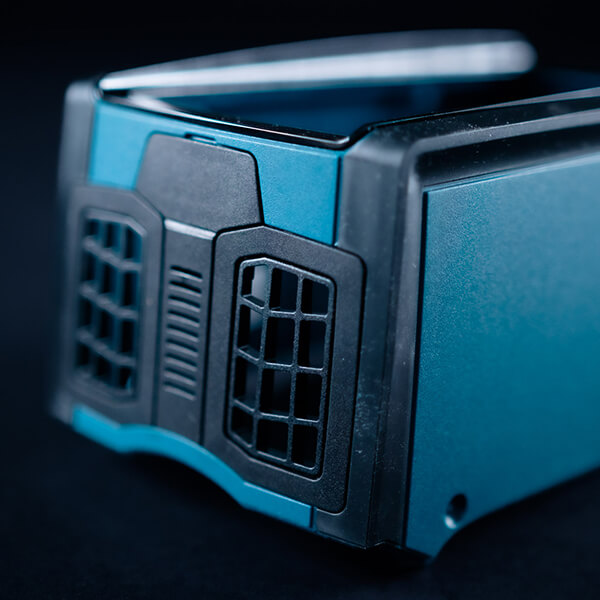
Beratungstermin
Wir beraten Sie gerne bei allen Fragen rund um die Themen Design, Konstruktion, Fertigung und Weiterverarbeitung von Spritzgussprodukten.
Angebot
Sichern Sie sich jetzt Ihr maßgeschneidertes Angebot für erstklassige Spritzgussteile!
Prospekt anfordern
Das Fertigungsverfahren von FUNK DREIDIMENSIONAL
FUNK DREIDIMENSIONAL setzt modernste Spritzgieß-Maschinen ein, um alle erdenklichen Anwendungen aus verschiedenen thermoplastischen Kunststoffen herzustellen. Besonderheiten wie Oberflächenveredelungen, Lackieren oder Bedrucken sowie das Verpacken in individuell gestalteten Schmuckverpackungen werden gemeinsam mit zuverlässigen Partnern gelöst. Das Unternehmen überprüft ständig seine Fertigungs- und Montageprozesse anhand modernster Management-Tools und legt großen Wert auf kontinuierliche Verbesserung sowie regelmäßige Schulung seiner Mitarbeiter.
Insgesamt bietet FUNK DREIDIMENSIONAL einen umfassenden Überblick über die industrielle Fertigung von hochpräzisen Kunststoffteilen mithilfe modernster Fertigungsverfahren und Materialien. Bei der Arbeit helfen ihnen ihre jahrelange Erfahrung sowie ihre Branchenkompetenz im Bereich der Massen- und Einzelfertigung.
Bleiben Sie immer top informiert mit unserem Newsletter.
Sie erhalten exklusive Informationen, Angebote und Neuigkeiten direkt in Ihr Postfach.